Essential checks to make before installing road plates
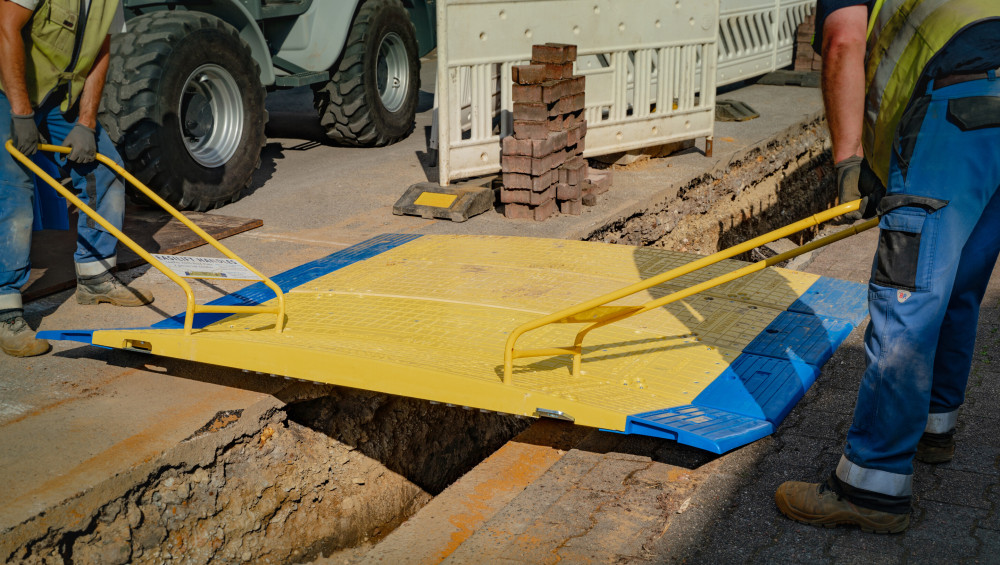
When carrying out work when digging trenches, it’s important to choose the right product to cover your excavations to make the site safe to access for pedestrians or traffic to access. This guide will highlight some of the main things you need to look out for when installing road plates.
Installing steel road plates
Steel road plates are usually installed on works where the plates do not need to be moved and are not usually suitable as temporary road cover. Steel road plates have a more complicated installation preparation process in comparison to composite road plates. In order to prepare to install a steel road plate some of the considerations you’ll need to make include;
- Assess the site: Evaluate the site confirming the steel road plates meet the load-bearing capacity needed.
- Survey the ground: When installing steel road plates it’s important to check that the area where the steel road plate is to be installed is free from debris to ensure that the road plate sits flat against the surface and can be secured. Make sure the ground is stable and compacted so that it can support the weight of the steel road plates.
- Arrange the correct tools and equipment: Prepare the necessary equipment and tools for handling the steel road plates, including lifting equipment, cranes, fasteners or any other additional materials required for securing the plates.
- Recessing: Recessing essentially involves fitting the road plate into a recess etched into the surface of the road. To do this you will need to use machinery to chip away the surface of the road.
- Pinning: Pinning is one of the main ways that steel plates are made secure when they are installed, this essentially consists of drilling through premade holes to secure the road plates to the road.
- Cold Patching: Cold patching is the practice of using asphalt to secure the road plate and reduce the size of the lip between the plate and the road to make a smooth transition for cyclists and motorists to cross the road plates. Installing asphalt requires tamping down to keep it secure which can be time-consuming.
Installing composite road plates
Composite road plates do need some preparation to install safely, but in general, they are much easier than steel road plates as they do not require the use of heavy machinery to install. The sloped edges also mean that there is no need to cold patch. To prepare your surface for installation, there are a few considerations you’ll need to make, such as;
- Assess the site: Evaluate the site confirming the composite road plates meet the load-bearing capacity needed.
- Survey the ground: Clear the installation area of any debris, obstacles or loose materials and ensure the ground is level and compacted properly.
- Arrange the correct tools and equipment: Unlike steel road plates, it’s unlikely that you’ll need any heavy lifting equipment or cranes to lift the composite road plates into position. For example, you can lift the LowPro 23/05 easily with EasiLift Handles.
- Bolt into place: For extra security, you can use bolts or drop pins to secure the road plates in place.
Essentially, composite road plates are considered as easier to install and there is minimal preparation needed due to their lightweight nature, and because they don’t require the use of heavy lifting equipment to install like steel road plates do.
How can Oxford Plastics help?
Here at Oxford Plastics, the LowPro range of composite road plates are designed as an easier to use alternative to steel road plates. Our road plates are designed to link together in order to cover the full length of the trench and can easily be installed by hand.
Want to see how steel plates perform against composite road plates? Read our guide. Or if you’ve already made the switch to composite road plates, learn how simple they are to install here. If you’re ready to make the switch but need more information contact our helpful team today.
Related News
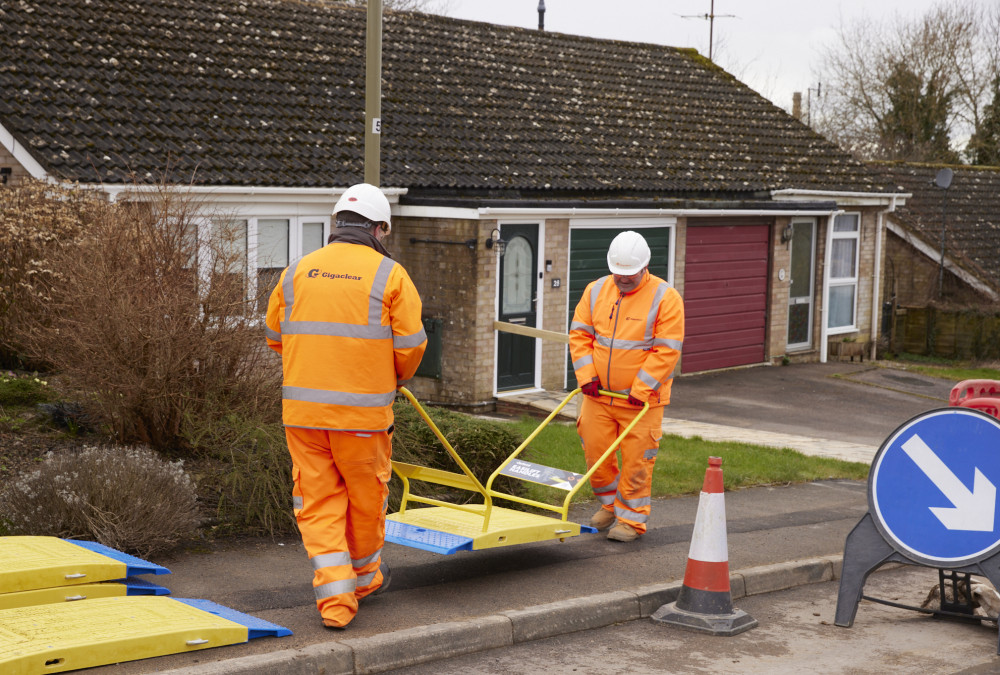
What happens on a product training day?
Here at Oxford Plastics our knowledgeable team is on hand to provide comprehensive training so that you can be confident in c...

Oxford Plastics Innovation for HAUC Compliant Products
Here at Oxford Plastics, our products are manufactured to the highest possible standards so that they not only comply with HA...
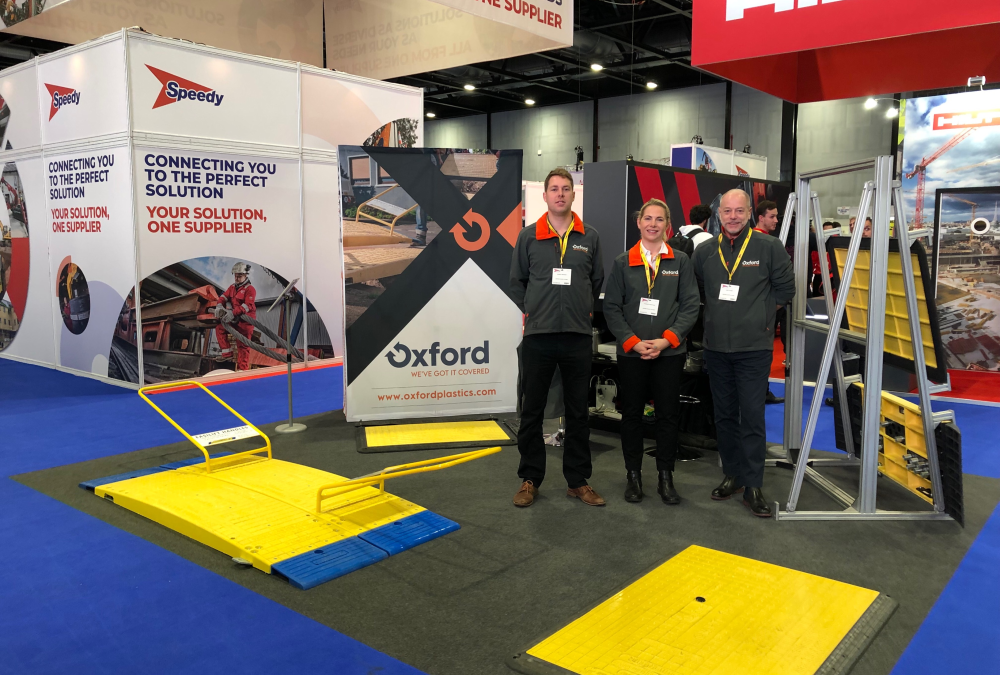
Health and Safety Calendar 2024
Safety has been at the core of innovation at Oxford Plastics for the last 35 years, and as we enter 2024, we’ve compile...